Walter Knoll – the modern furniture brand – stands for the highest standard in design and the untiring quest for excellent quality.
1865- 2015
150 years Walter Knoll. Something to be proud of. Yet, how does a business so steeped in tradition manage to stay on course? A trip to the Herrenberg company provides a glimpse. A first visit to the Swabian town leaves you breathless. Between the train station and historical brick buildings, a modern concrete waler construction with glass facades to the north and south rises up in the centre of town – the Walter Knoll Markenland.
On the ground floor, you can watch eager upholsterers through the glass fronts that reach to the floor. They are covering seat frames with leather, fitting fine Aniline skin over sofa elements, and stuffing matching cushions with filling. Of course, they make passers-by feel as if they’re a part of this valuable craft. Some of the outsiders greet and exchange familiar winks with employees on the inside.
It hasn’t always been like that. Until a good ten years ago, the traditional company’s upholstery and sewing work was in closed-up workshop halls But the new building in 2006 brought a wind of change with it, everything had to be different: open and transparent – for employees, but also for the surrounding residents and of course for visitors from around the world. This year, the Herrenberg company celebrates 150 years of existence. The former leather business of the founder Wilhelm Knoll is now considered the furniture brand of modernity and has become a successful global player. And this is not by accident.
The high standard of design and the everlasting quest for excellent quality
gave rise to developments like the patented Antimott spring in the 1930s or the Prodomo steel pipe furniture; concepts that made furniture history.
With the Rolf Benz family purchasing the company in 1993, two of Germany’s renowned furniture dynasties finally merged. Director Markus Benz trusts in classic values contemporarily executed. It sound so simple, yet actually requires lots of experience. “Manu factum” is the magic word. So why not display what you are capable of? But unlike many manufacturers that set up artificial workshops, the company does not intend to glorify old processes by revealing the manufacturing steps.
Walter Knoll is about quality.
A quality that can only be created by the ingenious interaction between specialist know-how and the latest technology. As Markus Benz puts is so aptly: “The handiwork of the upholsterers and seamstresses requires strength and an expert touch.” The idea of the glass “factory” has proven itself.
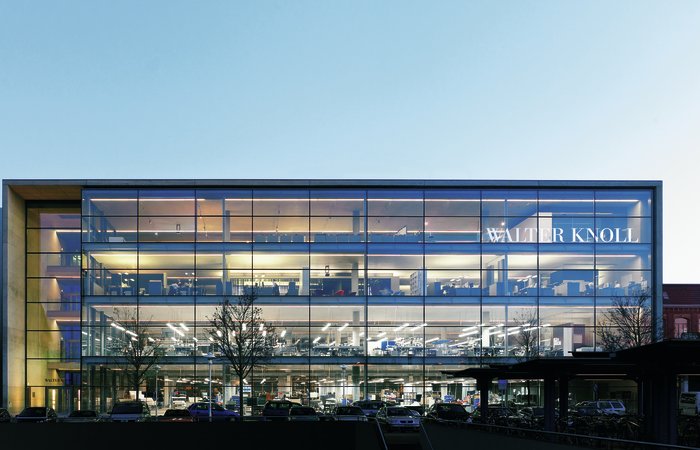
The employees enjoy the work atmosphere in the light-flooded rooms. Rooms of equal size are built over four floors, production rooms, offices, and exhibition spaces. The first floor houses the cutting and sewing shop. The seamstresses work there, depending on season and order intake. Under their nimble fingers, individual pieces of leather become a custom-made cover.
Every single state-of-the-art machines has a specialised function. Some examples: a seam at a 90-degree angle, a classic suitcase seam, a double seam, or a flush decorative seam like the ones found on all the Isanka models. The air-cooled machine stitches through 5mm-thick core leather, guided by the steady hand of a professional.
The slightest disturbance will spoil the quality of the decorative seam. It is astonishing that new seams are still being developed in the 21st century. Yet, a constant stream of new design ideas present the master craftsmen with new challenges. And spur them on. The high quality standard is also expressed in the choice of materials.
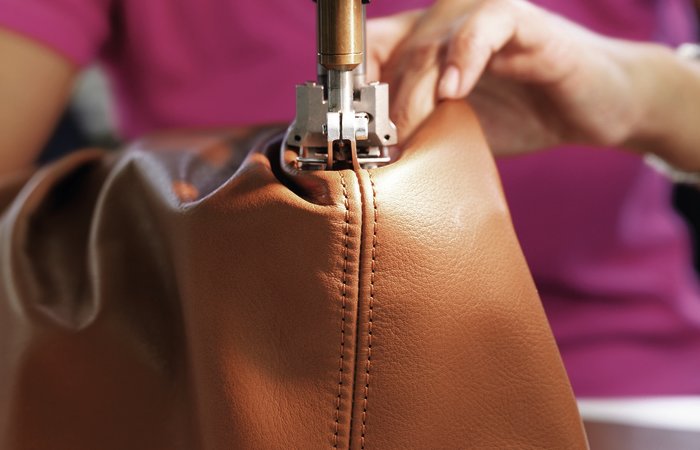
Walter Knoll products are made of around 70% leather.
The hides are a waste product of livestock farming and are sourced exclusively from young European bulls. The hides are exclusively tanned, oiled, and stained in Europe’s best tanneries. When the batches of leather hides are delivered, the careful assessment process begins: colour matching with the original Walter Knoll pattern, inspecting for the tiniest mosquito bites, horn Injuries, or other signs of the unfettered life of two-year-old bulls. Not one small wound escapes the experienced eyes of the employees. Defective spots are marked are marked and cut out by CAD and laser.
From goods receipt to finished leather cover, each hide passes through four quality control tests. In between, the hides are stretched, sharpened, split, pierced, or embossed. Skilful hands supply it with piping or zippers before the custom-made suit is sent to the ground floor for the “wedding”, which is what Walter Knoll employees call the final unification of white cushions and leather covers.

Spot visits to the manufacturer are a matter of course for interior designers, planners, and dealers. But customers can experience the manufacturing process of the products as well, from the development of the concept, through cutting, sewing, and upholstery, up to final delivery.
If you decide on a piece of Walter Knoll furniture, you don’t do it in passing.
It happens quite often that interested persons appear in Herrenberg to see “their” piece of furniture on site. Or because they just want to know where the carefully crafted piece, that will lovingly seat their families and friends in future, comes from. If you want to perfect masterful quality, you have to be ahead of the times – and inspire future generations with your products. How to explain to future customers where the value and quality of a product lie? It doesn’t seem to be a problem for Walter Knoll. Markenland with its glass facades was a clever step in the right direction. Because it reflects one thing above all: that they really love their own products.
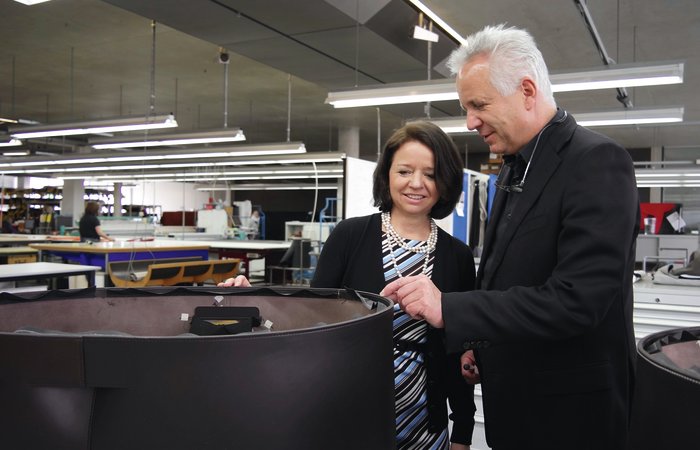
Photos: © Emil Benz